Imagine getting to do what you love and getting to be your own boss. Does this sound like a dream come true? It’s not too far fetched of a concept when you have a creative vision and a can-do attitude. Theresa Harmon is a prime example of what talent and hard work can amount to. She was kind enough to share with us her sewing history and how she came to run her own small business using her Sailrite® Fabricator® Sewing Machine.

For Theresa, sewing and crafting have been a passion since she could use crayons and paper. But sewing started in a 7th grade home economics class, and 48 years later, her creative drive has opened up more doors for her than she could have ever imagined. “In 2006, I bought my first embroidery machine. Upon returning to the store for new owner classes, I was solicited about a sewing job. There was a local woman restoring a historic carriage house in a bed and breakfast. She needed a seamstress and I needed to pay for my expensive machine! After successfully sewing window treatments, cushions, pillows and slipcovers for her, I decided to start my own shop called All the Trimmings. This was the first incarnation of my business, and so far I’ve sewn for interior designers, decorators and, of course, my own customers. The second incarnation of my shop started in 2018 and is still going strong today. ”
“My goal with sewing is to satisfy my creative, social and entrepreneurial needs while fabricating one-of-a-kind soft furnishings for a niche retail market. I’m a one-woman workroom! I make custom furnishings like pillows, seat cushions, curtains, drapes and more that aren’t available in the mass-retail market.”

Now you might be wondering where the Sailrite Fabricator comes into play in all this. Well, a small sewing business would be nothing without a trustworthy machine to build the business on. Theresa was more than willing to share how her journey intersected with the Sailrite mission to empower DIYers. “My reason for choosing Sailrite and the Fabricator was the customer service, hands down. At the time, I was shopping for machines and working as a sales associate for another sewing machine dealer who taught new owners how to use their machines. I quickly understood how important it was for customers to learn how to use their new sewing machines in order for them to feel satisfied with their purchase and be confident sewers.”

“The Fabricator had all the built-in features I wanted, like a built-in walking foot and the ability to go slow while still using full power. These features are critical for achieving meticulous upholstery detailing. Another plus is the access to all the free Sailrite videos and the promise of tech support via email and phone. Having my Fabricator (which I’ve named Oz) gives me a lot of confidence in my ability to turn out professional work!”
Theresa has made tons of incredible projects for clients with her industrial sewing machine, and both the results and the customers can attest to her talent. You might’ve even seen some of Theresa’s work featured on our Sailrite website or our Instagram page! So far she’s made things like vinyl banquette cushions, window seat cushions, pillows, breakfast nook seating and more! Theresa recalled one of her more daunting DIY projects, and one that she is most proud of — a revamp of a mid-century papasan chair. A local interior designer reached out to her about the chair and she was able to tackle the project with a little ingenuity and elbow grease from the Fabricator.
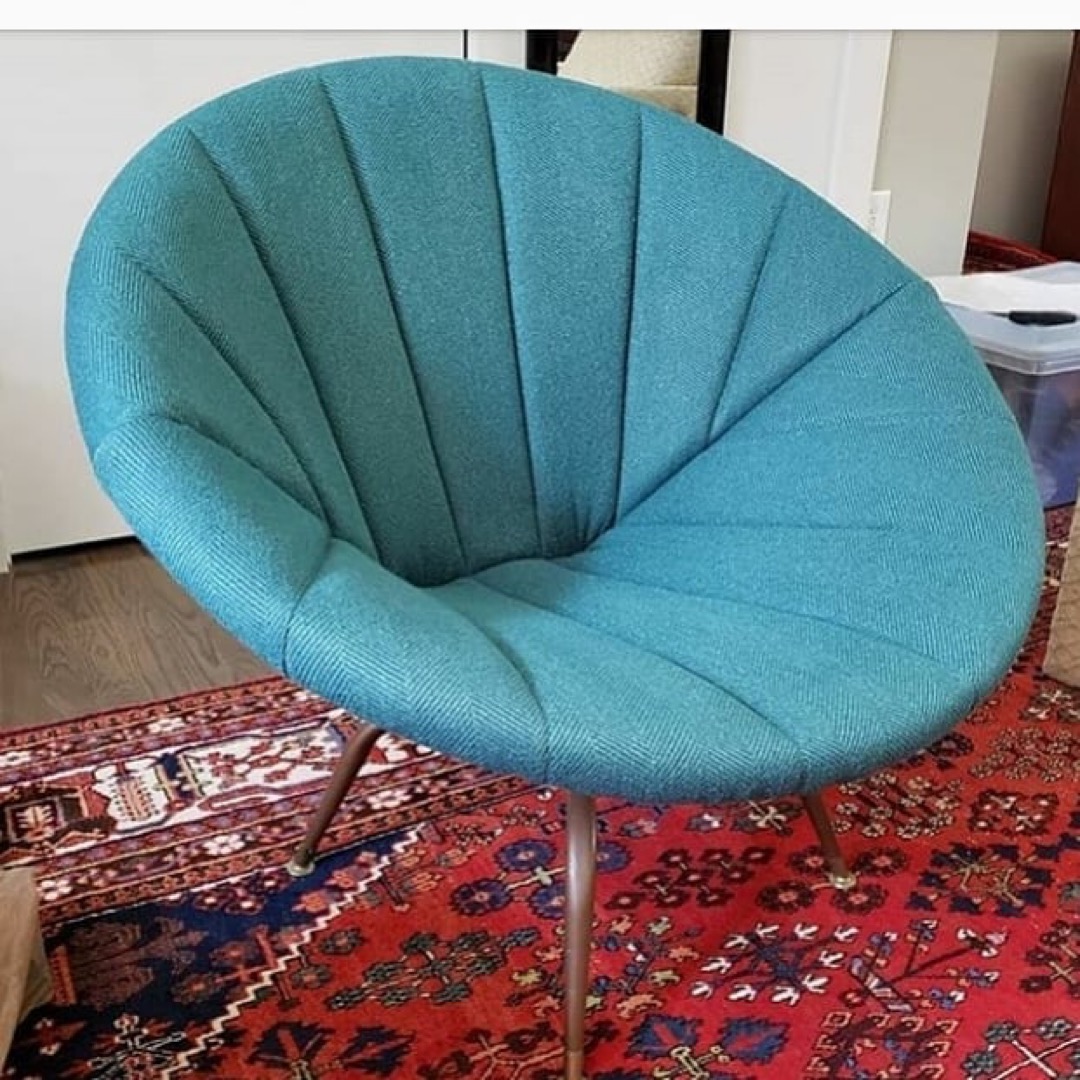
After speaking with Theresa, we had a few more questions about her DIY successes. Luckily, she had answers!
Q: What is it about the DIY sewing lifestyle that you enjoy the most?
A: I find the process of creating something that’s never existed before to be fascinating. To be able to get paid to do something I love and decide when I will work is an irresistible combination.
Q: Do you have any words of wisdom for someone thinking of starting to sew their own projects?
A: Don’t be afraid of failure. I believe all of us learn best through our mistakes. Perfectionism and comparison both squelch our creativity. Every person’s journey is unique; therefore, there are no absolutes to success other than trying your best while continuing to practice and try new things.
Q: What projects do you see yourself sewing in the future?
A: I’ve made a lot of purses in the past but never one from leather. Since I have some scraps and I know Oz (my Fabricator) will have no problem sewing through it, maybe a leather tote bag is in my future!
Does the DIY lifestyle still sound like a pipe dream to you? Theresa’s story is proof that you can learn the tools of the trade and, with the right sewing machine and support, you, too, can sew projects for every area of your life. Who knows, you might even get good enough to be your own boss! Anything is possible when you embrace your inner creativity and put in the work. And Sailrite is here to help you every step of the way.
Who We Are
Sailrite is your one-stop DIY shop! We are a passionate crew of do-it-yourselfers who strive to equip you with the supplies and how-to knowledge you need to tackle your next project. Do you want to learn upholstery, leatherwork, canvaswork, hobby sewing, bag making or more? We have the fabric, tools, hardware, sewing machines and notions you need to master any DIY. And even if you’ve never sewn before, our tutorials and how-to videos are designed for beginners and experienced crafters alike.
Start your DIY journey today: www.sailrite.com