Which came first, the chicken or the coop? For Genelle Hitchman, it was a flock of chickens — which led to a unique wagon-style coop that would change her life.
Genelle and her husband, Todd, are die-hard DIYers with a 10-acre homestead in Texas. Aptly named Hitchman Homestead, the land hosts not only the family’s home, but a thriving business building pioneer-style wagons tailored for different uses. Genelle sews the bonnets (fabric tops) for these wagons with her Fabricator® sewing machine and other Sailrite® materials.
Such a unique business must be the result of thorough planning, right? Well, not quite. Genelle and Todd never intended to start a covered wagon business. Instead, it was a surprise that came from Genelle’s dream of owning chickens.
“Growing up, my grandfather had a garden and chickens. I have happy memories of collecting fresh eggs from his small coop. I have always wanted a garden and chickens of my own, but it was always just out of reach.”
Before moving to Texas, the Hitchman family lived in a crowded California city. They weren’t able to build the self-sustaining lifestyle they wanted there. “When we bought our home together in California on a tiny lot (so little room for gardening), our city had many restrictions on ‘homesteading’ activities — so chickens … were a no-go,” Genelle remembered.
In addition, the couple’s demanding jobs left them burned out. They didn’t get much free time to spend with each other or their seven children. After years of nonstop stress, they’d had enough. “We decided that we wanted to stop ‘living to work’ and start ‘working to live.’”
Genelle and Todd knew they’d have to completely overhaul their lives to become homesteaders. But they were so ready for a change that they threw themselves into the prep with a will. “We started planning a year ahead of time,” Genelle said. “We wound down our careers in California. I learned homesteading skills. We had to find a suitable area and property.”
Their property search took them to the wide-open spaces of the Texas Hill Country over a long weekend. “We went with the intention of just getting an idea of the area, but found our dream homestead on day two of our trip. We were signing purchase contracts as we boarded the plane home!” Genelle told us.
After the perfect property fell into their laps, Genelle and Todd knew their move was meant to be. The family settled in Texas in 2018 and spent the next few years setting up their homestead. It now includes chickens and goats, a garden, a composting system, and much more.
The Wagon Business Gets Rolling
The homestead’s chicken flock was the inspiration for the first wagon Genelle and Todd made. Genelle told us that she and Todd were watching the chickens one day when Todd said, “Boy, I sure do like having chickens, but it’s a shame their stuff is so ugly.” The store-bought coop and run the chickens had at the time didn’t fit with the homestead’s décor.
Todd decided to change that. “The next day, I awoke at [3 a.m.] to find him at his drafting table,” Genelle said. Todd showed her a sketch of a coop modeled after a covered wagon and asked, “Wouldn’t you rather see this in the yard?”
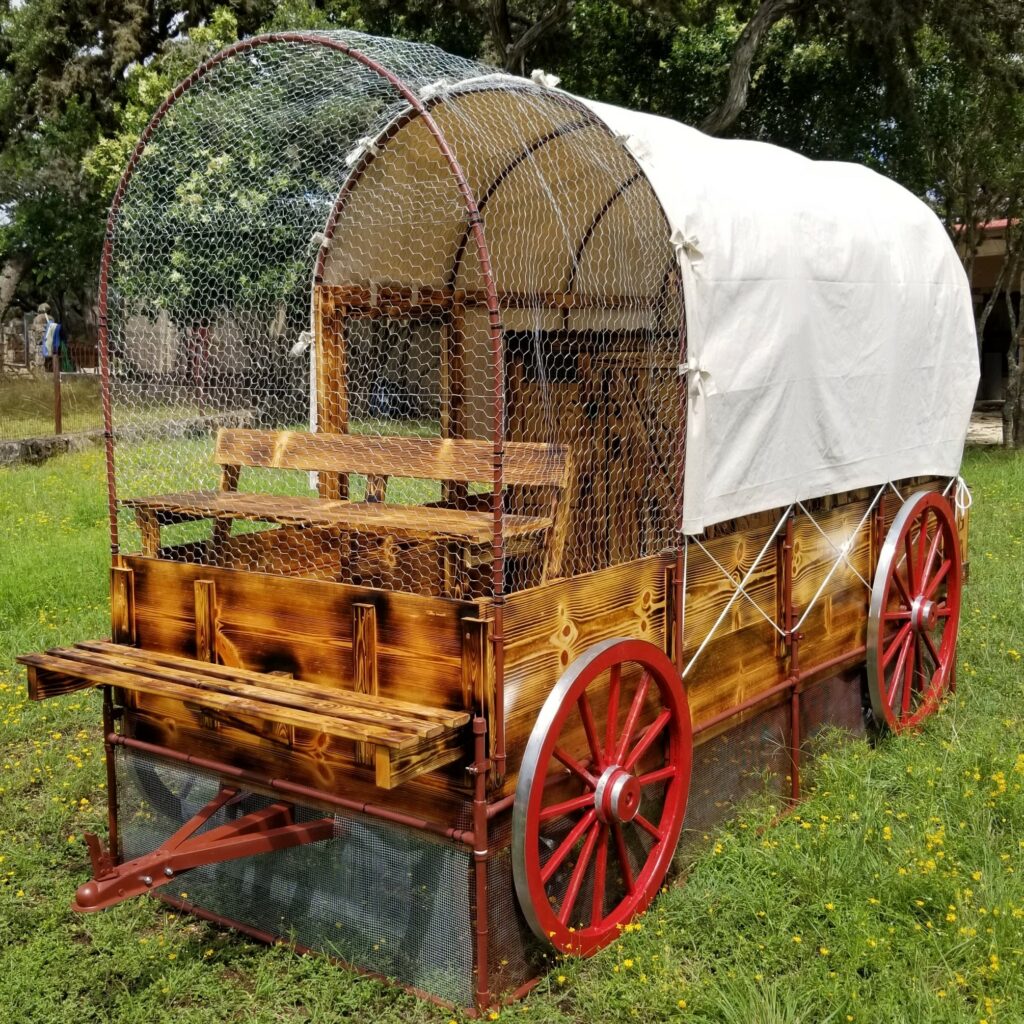
Why a covered wagon? Genelle told us that “Todd has always been a fan of Old West movies. He … often pauses shows to get a closer look at wagon details. Anytime we see an antique wagon, we stop and look. There’s a lot of wagon art in our house.”
Genelle agreed that a wagon-style chicken coop would fit right in with the homestead. The “Cluck Wagon” came together over the next few weeks. Todd built the wagon while Genelle sewed a suitable bonnet from a hardware store drop cloth.
Once the wagon was ready, the flock moved into its new home. “It was adorable,” Genelle gushed. “I took some pretty photos. … I shared my photos on Facebook in my chicken groups. Overnight, my photos went semi-viral. I woke up to about 6,000 likes and shares, and an inbox full of messages [like], ‘That is the cutest thing I’ve ever seen, I want one!’”
From there, the unintentional business took off. “We built a few wagon-coops delivered more or less locally and then started getting requests. ‘I don’t have chickens, can you just do the wagon?’ ‘Can you make it a farmstand?’ ‘Can you make it into a kid’s bed?’ So we did!” Genelle said.
Frontier Sewing With the Fabricator
The demand for custom wagons led Genelle to Sailrite in early 2023. At the same time, she realized that her home machine wasn’t strong enough to sew wagon bonnets. “We’ve been … progressively getting more elaborate and authentic with the bonnet canvas,” she told us. “Early this year, I had really been struggling … getting the heavy wagon bonnet canvas through [my small machine].”
But then, a customer asked for something even sturdier than the canvas Genelle was using. “We took on a build where the client … wanted a waterproof [marine grade] fabric, which I found on the Sailrite site. After ordering a sample, I concluded that my current machine was not suited for this fabric.”
Luckily, the solution wasn’t far away. “Sailrite … carried the industrial machines I would need to work at this level.” After comparing her options, Genelle decided on the Fabricator. When we asked for her thoughts on the machine, she described it in two words: “Game changer.”
The Fabricator has revolutionized Genelle’s work. “Going from a budget, old home sewing machine to a top-of-the-line industrial beast took some getting used to. … Now that I have a few projects under my belt — I LOVE IT. Using the Fabricator has cut my bonnet construction time in half. I am also very proud of the quality of my bonnets now, and I know they will hold up and look professional.”
Genelle has been back to Sailrite several times for other supplies and project help. “Sailrite has been amazing from the beginning,” she said. “It’s so much more than just a supplier. The videos and guides are wonderful tools for me to learn as I work with new materials and my new Fabricator machine.”
Genelle’s Fabricator has allowed her to customize each bonnet to the wagon’s planned use. “Our wagons are not antique restorations. They are new builds, intended to look like an antique wagon but useful for modern purposes,” she explained. For example, many customers have ordered wagons as vendor stalls. However, the fully enclosed bonnets that authentic frontier wagons had wouldn’t work for this purpose.
True to her self-reliant nature, Genelle used her Fabricator to come up with a solution. “I have created our own stylized bonnets (with Sailrite fabric!) that … still look the part without being ‘authentic’ covers.”
The Fabricator also gets to sew a huge range of other projects on the homestead. Genelle has been sewing since childhood. “My mother taught me the basics of sewing at about 10 years old,” she told us. “I was a very small child — and as a teen, when my fashion sense began to develop ahead of my growth, I loved that I could make fashionable clothing in my size.”
Her passion for the craft has only grown since then, and she has plenty of ideas for DIYs. “I still sew anything and everything. Recently, I have been repurposing our burlap green coffee bags into rustic farmhouse Christmas decorations … I alter clothing. I sew a lot of accessories for our wagon builds — wheel skirting, sink skirting, basket lining … anywhere there needs to be a ‘touch of textile’ to finish the look. My favorite projects have always been costumes.”
The freedom that drew her to homesteading is also one of her favorite things about sewing and her DIY lifestyle. “Our only limitation is our willingness to do anything,” she explained. “We can build, do and produce whatever we want with almost no restrictions.”
Advice for Building a DIY Business
The Hitchmans’ business is the true fulfillment of their years of dreaming. “As we were planning our move years ago, we had a conversation that went: ‘If you could do anything, what would you do?’” Genelle’s answer was raising chickens. Todd said he wanted to make art. As it turned out, their wagon- and coop-building business includes both of these passions.
“When we came [to Texas], we didn’t anticipate the direction things would take! If you’d have told me six years ago, ‘Hey, you’re going to build pioneer wagons for a living,’ I’d have thought you [were] crazy. But here we are,” Genelle said. “It’s really awesome to see our hearts’ desire become tangible and to make a living doing something we both love.”
We asked Genelle what she would say to someone looking to quit a restrictive job and start a DIY business like she did. She gave this advice:
“Get out and get involved in your local farmers market or maker/crafter community. Even if you can’t get a booth [or] table yet, go look and learn. See what people are buying. What do they want? What are they not buying? What isn’t being offered? Look at price points. Displays. What would you want to see as a buyer? None of this costs anything.
“Then start small. Use what you have. Do a thing, sell a thing. … Listen to your customers. Improve the thing. Sell another thing. Repeat.”
Genelle and Todd have certainly proven that this process works. And with big plans for Hitchman Homestead’s future, we know that they’ll continue DIYing their dreams. If you’d like to check out more wagon builds and see what Genelle is making with her Fabricator, you can follow her on Instagram at @hitchmanhomestead.
Genelle, thank you for sharing your story and for your encouraging advice. We’re delighted that the Fabricator and other Sailrite products are helping you achieve such great success! We wish Hitchman Homestead nothing but the best in the future.
Who We Are
Sailrite is your one-stop DIY shop! We are a passionate crew of do-it-yourselfers who strive to equip you with the supplies and how-to knowledge you need to tackle your next project. Do you want to learn upholstery, leatherwork, canvaswork, hobby sewing, bag making or more? We have the fabric, tools, hardware, sewing machines and notions you need to master any DIY. And even if you’ve never sewn before, our tutorials and how-to videos are designed for beginners and experienced crafters alike.
Start your DIY journey today: www.sailrite.com